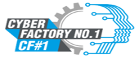
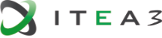
CyberFactory#1 (CF#1) aims at designing, developing, integrating and demonstrating a set of key enabling capabilities to foster optimization and resilience of the Factory of the Future (FoF).
It embraces technical, economic, human and societal dimensions at once with 28 partners from seven different countries, which are pilot users, suppliers as well as research and academic organizations.
CF#1 is a catalyst project – therefore, it will supplement and develop current enabling technologies of the Industry 4.0 further to key capabilities in relevant application scenarios and verify their usability in realistic use cases. Specifically, it aims to develop key capabilities in the area of (1) Factory System of Systems modelling; (2) FoF Optimization; and (3) FoF Resilience.
The key problem addressed by CF#1 is the need to conciliate optimization of the supply and manufacturing chain of FoF with the need for security, safety and resilience against cyber and cyber-physical threats.
In CF#1 current enabling technologies of Industry 4.0 will be supplemented and developed further to key capabilities in relevant areas. These key capabilities will be mapped in relevant application scenarios and their usability will be verified in realistic use cases, reflecting the variety of possible new factory types like user-centric plant or learning factories and taking into account business model shifts like turning products into services or developing data services on top of manufacturing activities.
Factory of the Future Optimization: cluster of technology developments enabling to optimize manufacturing and supply chain processes and develop data-centric business models
- Real time sensing, tracking & supervision of tools, materials and humans in the supply chain, which can be used to identify the state and evolution of the factory of the future, to optimize their behavior and to detect anomalies and take appropriate action to control the anomalies
- Data-lake exploitation: enabling to build new business opportunities based on big data analytics over the manufacturing data thread
- Optimization of human / machine collaboration on the shop-floor with the help of AI-methods to facilitate “learning” by human operators and to allow autonomous “additional learning” while ensuring the safety of people and machines.
- Distributed manufacturing capability: enabling to optimize the distributing of production load over a network of factories or fab-labs in real time
MKT Dairy use case introduces a new integrated platform-based concept for cheese manufacturing
Customer Benefits of the concept
- Flexible for product quality changes
- Scalable for future production increases
- Shorter installation and production start-up time
- Delivered fully tested and integrated from manufacturer
- Small footprint on dairy floor
- Lower service cost and easier maintenance compared to traditional dairy production lines
- Continuous cheese manufacturing process
For more information of Cybersecurity project, please visit https://www.cyberfactory-1.org
If You are interested to know more about MKT Dairy, please contact our Cheese manufacturing expert
Mr. Henri Granberg, henri.granberg@mkt-dairy.fi